Comprehending the Key Elements and Repair Service Techniques for Packaging Machine Upkeep
Efficient maintenance of product packaging equipments rests on a complete understanding of their essential components, consisting of the framework, drive system, and securing systems. Recognizing common upkeep issues, paired with the execution of preventative methods and troubleshooting strategies, can substantially improve machine dependability. Additionally, the choice of repair service practices, including using OEM components and the importance of qualified specialists, plays a crucial function in lessening downtime. To really comprehend the complexities of these systems and their upkeep, one have to think about the more comprehensive implications of ignoring these important methods.
Key Components of Packaging Makers
Product packaging machines consist of several essential elements that collaborate to make certain effective and efficient packaging processes. At the core of these devices is the framework, which supplies structural stability and houses the various operating parts. The drive system, usually a combination of electric motors and equipments, assists in the activity of parts, making it possible for specific procedure throughout the packaging cycle.
Another vital part is the conveyor system, which delivers products through various stages of the packaging procedure. This is usually enhanced by sensing units and controls that keep an eye on the placement and speed of items, guaranteeing synchronization and minimizing mistakes. The filling up system is vital for accurately dispensing the right amount of product into plans, whether in fluid, powder, or solid form.
Securing mechanisms, consisting of warm sealants or adhesive applicators, play a crucial function in securing bundles, avoiding contamination and prolonging service life. In addition, identifying systems are essential for giving needed item details, guaranteeing conformity with policies. Ultimately, the control panel, furnished with easy to use user interfaces, enables drivers to handle machine features, display performance, and make changes as needed, making sure optimal performance and performance in packaging procedures.
Common Maintenance Problems
Effective operation of product packaging equipments relies greatly on regular maintenance to avoid common problems that can interfere with manufacturing. Amongst these issues, mechanical deterioration prevails, specifically in components like electric motors, seals, and conveyors, which can bring about unexpected downtimes. In addition, misalignment of parts can result in inefficient procedure, creating items to be inaccurately packaged or damaged during the process.
One more typical upkeep issue entails the build-up of dirt and debris, which can conflict with the device's sensors and relocating parts. packaging machine repair service. This not just affects performance yet can also position security threats. Lubrication failures can lead to raised rubbing, resulting in getting too hot and eventual element failure.
Electrical troubles, often coming from loosened connections or damaged electrical wiring, can interrupt machinery features, causing considerable production delays. Software program glitches due to inappropriate arrangements or obsolete programs can hinder the machine's procedure, requiring prompt intervention. Attending to these typical maintenance issues proactively is crucial for guaranteeing optimal performance and long life of product packaging equipment.
Preventative Maintenance Techniques
Implementing preventative maintenance techniques is critical for sustaining the efficiency and dependability of product packaging equipments. These techniques incorporate a methodical strategy to upkeep, concentrating on the routine assessment and servicing of devices to preempt possible failings. By adhering to a set up maintenance program, operators can determine wear and tear on elements before they cause considerable failures.
Crucial element of a preventative maintenance technique consist of routine evaluations, component, lubrication, and cleansing replacements based upon producer referrals. Using checklists can streamline this process, guaranteeing that no necessary jobs are neglected. Additionally, keeping exact documents of maintenance tasks help in tracking the equipment's efficiency gradually, helping with notified decision-making relating to future upkeep needs.
Training staff on the relevance of preventative maintenance improves conformity and cultivates a culture of proactive care. Executing a predictive maintenance element, using data analytics and sensor innovation, can further optimize equipment performance by predicting failures before they take place.
Troubleshooting Techniques
When confronted with malfunctions or inadequacies in packaging makers, utilizing organized troubleshooting strategies is essential for determining and settling issues swiftly. The very first step in effective troubleshooting is to develop a clear understanding of the maker's functional criteria and efficiency metrics. This entails evaluating the machine's specs, along with any kind of error signals or codes presented.
Next, operators need to perform a visual examination, checking for noticeable indicators of damage, wear, or imbalance. This frequently consists of checking out sensing units, equipments, and belts to identify prospective root causes of breakdown. Gathering functional data, such as manufacturing rates and downtime logs, can also provide understandings into reoccuring issues.
When prospective troubles are identified, making use of a sensible approach to separate the source is critical. This may require testing individual parts or systems in a controlled manner. Participating in discussions with drivers that communicate with the machinery routinely can generate important comments regarding uncommon habits or patterns.
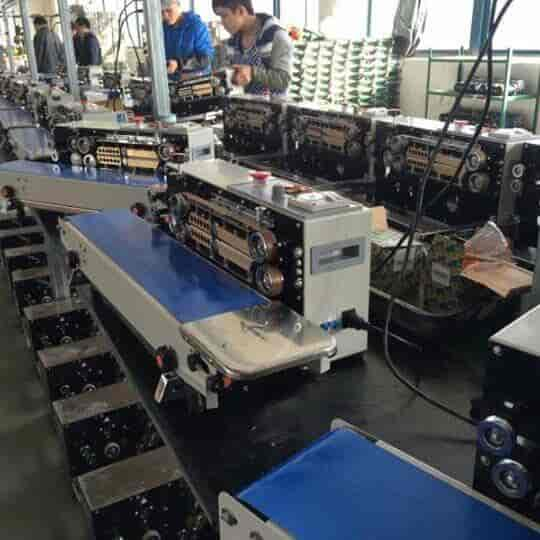
Repair Work and Substitute Finest Practices
A comprehensive understanding of repair service and replacement ideal techniques is discover this info here crucial for maintaining the long life and performance of packaging equipments. On a regular basis examining the problem of maker components permits for timely treatment, avoiding more significant concerns that can cause pricey downtimes.
When repair services are required, it is important to utilize OEM (Original Tools Producer) parts to ensure compatibility and efficiency. This not only preserves this the integrity of the device but additionally supports service warranty contracts. Additionally, it is advisable to preserve a stock of vital spare components to help with fast replacements and reduce operational disturbances.
For complicated repairs, engaging qualified service technicians with specialized training in product packaging machinery is suggested. They have the knowledge to diagnose concerns accurately and execute fixings efficiently. Recording all fixing activities and components substitutes is vital for maintaining a comprehensive maintenance history, which can help in future troubleshooting.
Last but not least, executing a positive strategy, including routine examinations and anticipating maintenance methods, enhances the dependability of packaging makers. By adhering to these finest methods, organizations can make certain ideal equipment efficiency, lower functional dangers, and extend devices life expectancy.

Verdict
To conclude, a comprehensive understanding of product packaging maker elements description and reliable upkeep approaches is essential for optimal efficiency. Routine inspections and using OEM components can substantially decrease downtime, while a well-documented upkeep history promotes aggressive treatment. Using licensed service technicians even more boosts repair work high quality and integrity. By applying these practices, companies can make certain the durability and performance of packaging devices, inevitably adding to enhanced operational efficiency and reduced expenses.
Effective maintenance of product packaging machines hinges on a detailed understanding of their crucial elements, consisting of the frame, drive system, and sealing systems.Effective procedure of product packaging equipments depends heavily on routine maintenance to stop common concerns that can disrupt manufacturing.Executing preventative maintenance methods is vital for sustaining the efficiency and integrity of packaging equipments. Furthermore, maintaining accurate records of maintenance activities help in tracking the machine's performance over time, promoting informed decision-making regarding future upkeep needs.
